Main hull construction ¹
Main hull construction part 1. After building and finishing the two floats, now it's the turn for the main hull. Part 1 is about the construction of the starboard half of the main hull. Please click on the images to open an extensive photo gallery of the various stages in the building process.

Beam Bulkheads
Before setting up the main hull, and while still having the room, I first made the beam bulkheads as these requires a special construction for the folding mechanism. A rather big laminating job with vacuum bagging. The first attempt is a bit disappointing, with epoxy everywhere, not only on the part, but also everywhere else. Because of a too sharp edge on the molded flange I pulled a big hole in the underside of the vacuum bag. Getting a wet vacuum bag airtight again is quite a job. While the resin clock continued it ended in a big mess. I left the workshop in my underpants, and with epoxy in my hair (it's shorter now). Now I know again why I dislike vacuum bagging and like the vacuum infusion so much. However, vacuum bagging is the way to go for this complicated laminating job. Or just hand-lay-up. But once used to the quality by a vacuum treatment, it's hard to be content with anything less. I am very comfortable using it. Click to open photo galleryAt the end, after eight vacuum bags, it's becoming more of a routine with less mess and better vacuum bags. Practice, practice ..........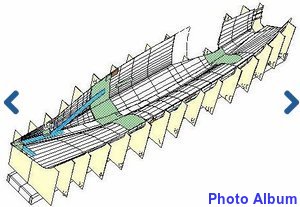
Setup first main hull half
This is one of these memorable stages. Not only the "real boatbuilding" work, at least the fun part has just begun in this stage, but more memorable is the fact that the hull fits in my small workshop as I had thought to myself. It's a close fitting and a relief at the same time. I've started with the starboard side of the main hull as the geometry of this hull half fits better in my workshop.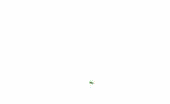
Layup dry laminate and infusion

About the video, the quality is not so good. Replacing it is still on my to-do-list, sorry about that.
Carbon folding anchors and folding system setup
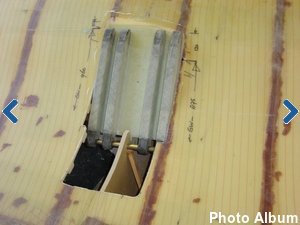
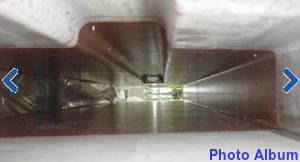
Daggerboard case
The daggerboard case is made of marine plywood and I discovered the hard way (at least after two failed vacuum bags) that the porosity of the plywood makes it impossible to make an airtight seal with sealant tape onto the wood. Something to remember for all wood builders. The vacuum infusion was done with two bags, one for the infusion and one for the vacuum integrity. A stopgap and not something to copy! Due to a lack of space in the workshop, my wife gave me permission to carry out the assembly and lamination of the daggerboardcase in the back of the living room....
Bulkheads and cockpit area
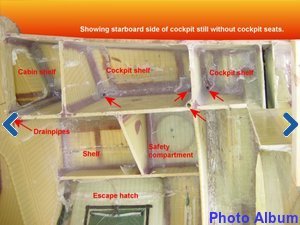

Unmolding the starboard main hull half
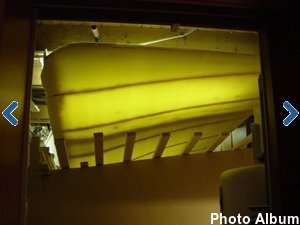
Interior layout

I finally decided about the layout of the interior.
The biggest change compared to the standard aft cabin layout is the galley on starboard instead of port. Main reason for this is that I still like "the office" on board, which lead to a rather conventional layout, in particular in combination with a quarter berth. Because of the galley on starboard the settee in front of this is now shorter, but still useable as a (sea) bunk with the feet through an opening in the cabin bulkhead. Above that the diesel oven is situated. Galley top can be extended by folding down the backside of the settee back.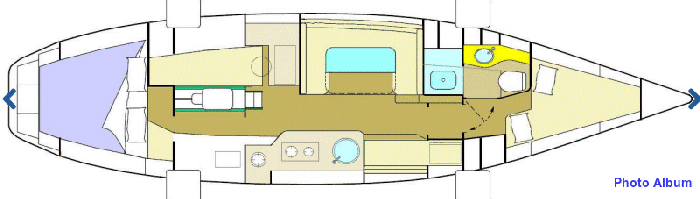
The dinette is now two meters wide and can be converted into a large spare double bunk. Also the shower is a little wider. Without rebuilding the interior this can accommodate six (with table down eight and with spare bunks in the floats even ten) Cooking is on a ceramic diesel stove and in addition to this a fully gimbaled single cylinder burner, positioned in a dedicated housing and well ventilated outside.
Of course the interior question is a matter of personal taste. I think this is a good sea going layout and at least for now this design gives me some peace of mind.
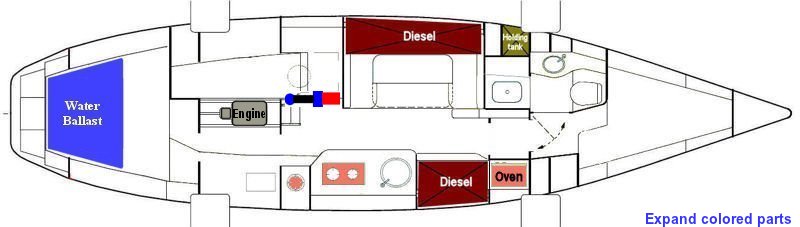
Systems

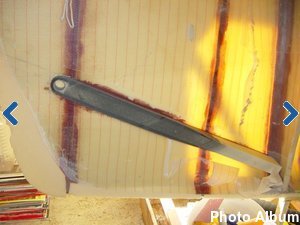
Carbon bobstay anchor
Some time ago I had a look on the composite department of Stork Aerospace and there I learned that they put a lot of effort in saving weight at the ends of airplanes and wings. Not a surprise of course but this reminded me of the quite heavy bobstay anchor in the bow of the F39. In spite of the fact that I prepared the piece of stainless steel to fasten into the bow, I decided to make a much lighter carbon one, almost in the same way as the carbon chainplates.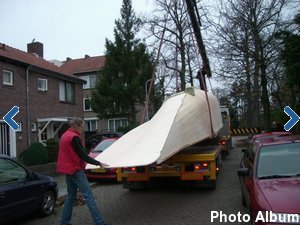
Moving to the new workshop
Quite unexpected and totally on the spur of the moment we bought a new house ..... Sometimes that one in a lifetime moment comes along, in our case a water villa with a jetty large enough for mooring our F-39 trimaran. So, the other "dream" we had, living in a house near the water, has become a reality now and we moved to our new place. Which means I had to gave up the workshop at home and move the boatbuilding project to a spacious workshop nearby, the workshop of our company.

A next phase in the construction of Fram begins. Occupying a part of the workshop of the company I work for is not forever. This means from now on I will focus on (partly) finishing the F39 and get her in the water to tie her up along the jetty of our new home. Further work on interior, hardware and rigging will be delayed till Fram has been launched and laying behind our new home.
« Previous Next » |